Welcome to My Blog!
I’m thrilled to have you here! Before we dive into the content, let’s stay connected. Join me on my social media platforms for more insights, community engagement, and regular updates. Here’s where you can find me:
📌 Facebook: Shandong Huaying International Trade Co., Ltd.
Now, let’s embark on this journey together. I hope you find the content here not only insightful and engaging but also valuable to your interests. Let’s learn, grow, and connect!
Table of Contents
Introduction
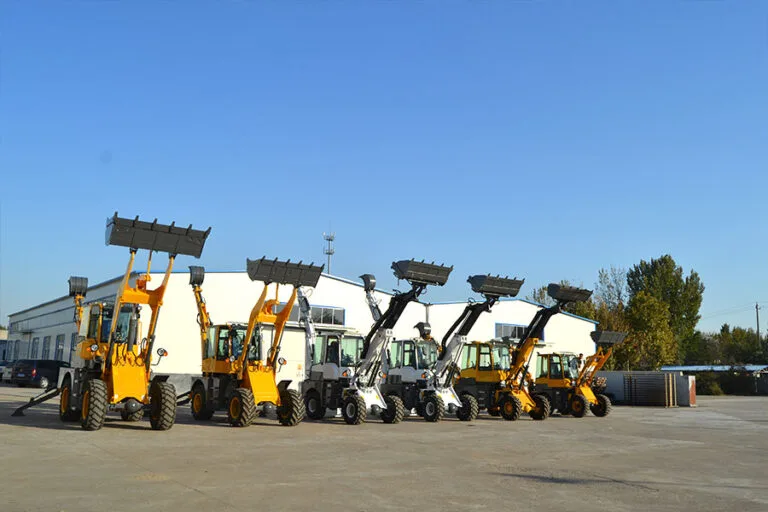
A 4 wheel loader is an indispensable piece of heavy equipment used for material handling, construction, farming, and various other industries. It is designed to lift, move, and load materials like dirt, gravel, or debris, making it an essential tool on any job site. However, despite their durability and robustness, 4 wheel loaders are susceptible to various issues that can lead to complete failure if not addressed in time. Regular maintenance and keen attention to operational performance can significantly reduce the risk of these failures.
In this article, we will explore six critical warnings that may indicate your 4 wheel loader is at risk of failure. Recognizing these issues early on can help you avoid expensive repairs, ensure optimal performance, and extend the lifespan of your machine.
Understanding the Basics of a 4 Wheel Loader
Before diving into the potential failures of a 4 wheel loader, it’s essential to understand how this machine operates. A 4 wheel loader is a versatile piece of machinery that operates with four wheels, providing it with the stability needed to perform various heavy-duty tasks. It is equipped with a large front bucket that can scoop and load materials, a hydraulic system to control lifting and lowering functions, and a powerful engine that drives the entire machine.
Some common components of a 4 wheel loader include:
- Engine: The heart of the loader, providing the power needed to perform various tasks.
- Hydraulic system: Responsible for lifting, tilting, and moving the bucket.
- Transmission system: Facilitates smooth movement of the loader across uneven terrain.
- Axles and tires: Provide stability and traction for movement.
Understanding these key components will help you better diagnose any potential issues that arise during the operation of your loader.
Critical Warning #1: Overheating Engine
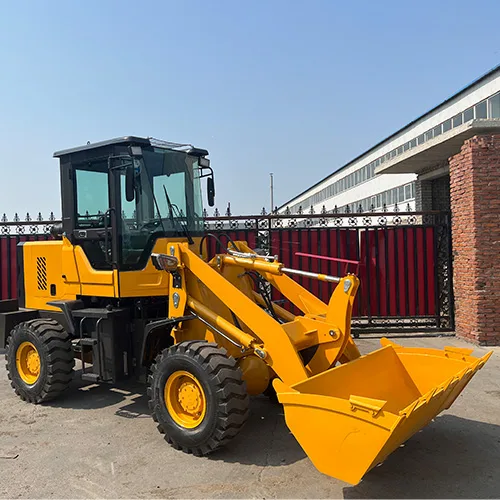
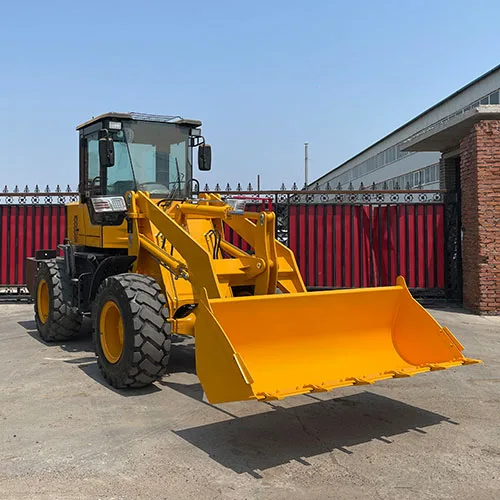
One of the most common problems with a 4 wheel loader is an overheating engine. This issue is particularly concerning because engine failure can cause a complete breakdown of the loader, resulting in costly repairs and significant downtime. Overheating typically occurs when the engine is not able to maintain a safe temperature due to insufficient cooling or blocked airflow.
There are several potential causes of engine overheating:
- Low coolant levels: Coolant is essential to regulate engine temperature. If the coolant levels are low, the engine may overheat.
- Radiator issues: A clogged or damaged radiator will prevent coolant from circulating properly, leading to increased engine temperature.
- Faulty water pump: The water pump circulates coolant throughout the engine. If it’s malfunctioning, the coolant won’t flow, and the engine will overheat.
- Blocked air filters: Air filters ensure that the engine receives adequate airflow. A clogged air filter reduces airflow, causing the engine to overheat.
Preventing overheating requires regular maintenance of the cooling system. Ensure that coolant levels are checked frequently, and any leaks are repaired promptly. Radiators should be cleaned regularly to prevent blockages, and air filters should be replaced or cleaned when necessary.
Critical Warning #2: Unusual Noises During Operation
A 4 wheel loader, when functioning correctly, should operate relatively smoothly with only the standard operational sounds. However, if you start hearing unusual noises such as grinding, whining, or clunking, it could be a sign that something is wrong.
These noises can be indicative of a variety of issues:
- Worn-out gears: The gears within the loader’s drivetrain can become worn over time, causing grinding or whining noises. This can significantly reduce the machine’s performance.
- Loose parts or bolts: If parts of the loader become loose due to wear and tear or inadequate maintenance, they can create loud noises as they rattle during operation.
- Hydraulic system issues: A failing hydraulic system can also produce strange noises, such as whining or whirring sounds, as it struggles to move the loader’s components.
Addressing unusual noises immediately is crucial. Ignoring them could lead to further damage to the machine, requiring expensive repairs or even replacement of key components.
Critical Warning #3: Decreased Hydraulic Performance
The hydraulic system in your 4 wheel loader is responsible for lifting, tilting, and performing various other functions. If the hydraulic system starts to underperform, it could cause the loader to struggle with lifting and moving heavy materials, which can lead to significant delays in work and productivity losses.
Several factors can contribute to a decrease in hydraulic performance:
- Hydraulic fluid leakage: Leaks in the hydraulic system can cause a drop in pressure, which directly affects the loader’s performance. Low fluid levels can also cause the system to malfunction.
- Clogged filters: Hydraulic filters are designed to remove contaminants from the fluid, ensuring smooth operation. Over time, these filters can become clogged, reducing fluid flow and causing the system to perform poorly.
- Low hydraulic fluid levels: If the hydraulic fluid levels drop too low, the system won’t have enough pressure to perform optimally. It’s crucial to check hydraulic fluid levels regularly and top them up as needed.
A significant decrease in hydraulic performance can halt work altogether, so it’s vital to address these issues promptly. Regularly inspecting the hydraulic system for leaks, replacing filters, and maintaining proper fluid levels will ensure optimal performance.
Critical Warning #4: Poor Maneuverability
A 4 wheel loader should be able to move efficiently and smoothly across uneven terrain. If you notice that your loader is becoming difficult to steer or is unresponsive to operator commands, it could signal a problem with the loader’s steering or drivetrain components.
Common causes of poor maneuverability include:
- Worn-out steering components: The steering system, including the steering rods and joints, can wear out over time, making it harder for the operator to turn the loader.
- Damaged wheels or axles: If the wheels or axles become damaged, the loader may struggle to move or turn, resulting in reduced maneuverability.
- Low tire pressure: Underinflated tires can cause poor traction and hinder the loader’s ability to move efficiently. Tires should be checked regularly for proper pressure.
Regularly inspecting the steering components, wheels, and tires for wear and tear will help prevent issues with maneuverability. Ensuring that tires are properly inflated and axles are in good condition is crucial to maintaining the loader’s ability to perform tasks on rough terrain.
Critical Warning #5: Excessive Vibration or Shaking
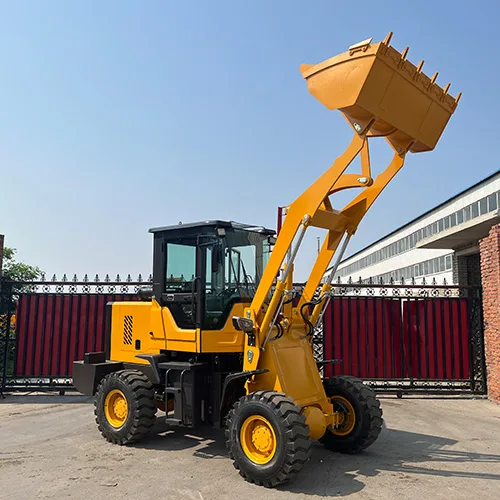
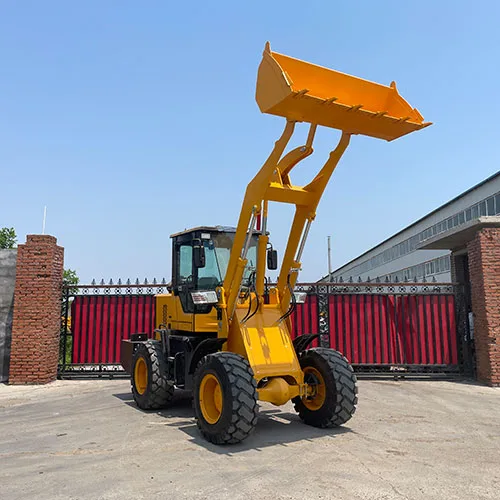
Excessive vibration or shaking during operation is another sign that your 4 wheel loader is experiencing mechanical problems. Vibration can not only make the loader uncomfortable to operate, but it can also lead to further damage to the machinery if not addressed.
Potential causes of excessive vibration include:
- Unevenly worn tires: Tires that are unevenly worn or damaged can cause the loader to vibrate while moving. Regularly inspect the tires for signs of wear and replace them as necessary.
- Faulty suspension system: The suspension system is responsible for absorbing shocks and vibrations. If the suspension components are damaged, you may experience excessive shaking during operation.
- Worn-out bearings: Bearings play a critical role in reducing friction within the loader’s mechanical systems. If the bearings become worn, it can lead to increased vibrations.
Addressing excessive vibration requires identifying the root cause, whether it’s tire wear, suspension issues, or bearing problems. Replacing worn-out parts and ensuring that the loader’s components are in good condition will help reduce vibrations and improve operator comfort.
Critical Warning #6: Electrical Failures
The electrical system in a 4 wheel loader controls everything from the ignition to the lights and dashboard indicators. If you experience electrical failures, such as flickering lights, dashboard errors, or difficulty starting the loader, it could be due to issues within the electrical system.
Common electrical issues include:
- Weak battery: A battery that is failing or has low charge can cause the loader to have difficulty starting or lead to intermittent electrical failures.
- Wiring issues: Damaged or corroded wiring can cause electrical malfunctions, including problems with the ignition or lighting system.
- Faulty alternators: The alternator is responsible for keeping the battery charged. If it fails, the battery will drain, leading to electrical issues.
Electrical problems can often be difficult to diagnose without proper equipment, so it’s essential to have the electrical system inspected regularly. Replacing worn-out batteries, checking wiring connections, and ensuring the alternator is functioning properly can prevent electrical failures.
Table: Common Issues and Their Solutions for 4 Wheel Loaders
Issue | Potential Causes | Recommended Solution |
---|---|---|
Overheating Engine | Low coolant, blocked filters, radiator issues | Regularly check coolant levels and radiator for leaks or blockages. |
Unusual Noises | Worn gears, loose parts, hydraulic issues | Inspect for worn parts, lubricate moving components, replace faulty hydraulics. |
Decreased Hydraulic Power | Fluid leakage, low fluid levels, clogged filters | Regularly check hydraulic fluid levels and replace filters. |
Poor Maneuverability | Worn axles, low tire pressure, damaged steering components | Replace worn parts and check tire pressure regularly. |
Excessive Vibration | Worn tires, faulty suspension, bearing damage | Inspect tires for wear and check suspension for damage. |
Electrical Failures | Weak battery, faulty wiring, alternator issues | Check electrical connections and replace damaged batteries or alternators. |
How to Maintain Your 4 Wheel Loader for Longevity
Preventing the issues mentioned above starts with regular maintenance and proper usage. Here are some tips for extending the lifespan of your 4 wheel loader:
- Regular inspections: Always check the loader before starting operations, looking for any signs of wear or malfunction.
- Lubricate moving parts: This reduces friction, which can prevent excessive wear and tear on mechanical components.
- Monitor fluid levels: Keep an eye on hydraulic fluid, coolant, and oil levels to ensure smooth operation.
- Tire maintenance: Inspect tires for wear, replace them when necessary, and keep them properly inflated to avoid issues with maneuverability.
Conclusion
A 4 wheel loader is a valuable investment for any operation, but like any heavy machinery, it requires proper care and attention to keep it running smoothly. By paying close attention to the six critical warnings discussed in this post, you can prevent major failures and avoid costly downtime. Regular maintenance, timely repairs, and prompt action when problems arise will ensure that your 4 wheel loader remains efficient and reliable for many years to come.
FAQ
How often should I perform maintenance on my 4 wheel loader?
It’s recommended to perform basic maintenance checks every 50-100 hours of operation, with more extensive inspections at regular intervals based on manufacturer guidelines.
Can I continue using my 4 wheel loader if I hear unusual noises?
No, continuing to operate your loader with unusual noises can cause further damage. It’s important to address the issue as soon as possible.
What’s the best way to prevent overheating in my 4 wheel loader?
Keep the coolant levels topped up, regularly clean the radiator, and replace any faulty components to prevent overheating.
How do I know if the hydraulic system is failing?
If the loader becomes sluggish or the lifting power is reduced, it could be a sign of hydraulic failure. Check the fluid levels and inspect for leaks or blockages.