Welcome to My Blog!
I’m thrilled to have you here! Before we dive into the content, let’s stay connected. Join me on my social media platforms for more insights, community engagement, and regular updates. Here’s where you can find me:
📌 Facebook: Shandong Huaying International Trade Co., Ltd.
Now, let’s embark on this journey together. I hope you find the content here not only insightful and engaging but also valuable to your interests. Let’s learn, grow, and connect!
Table of Contents
Introduction
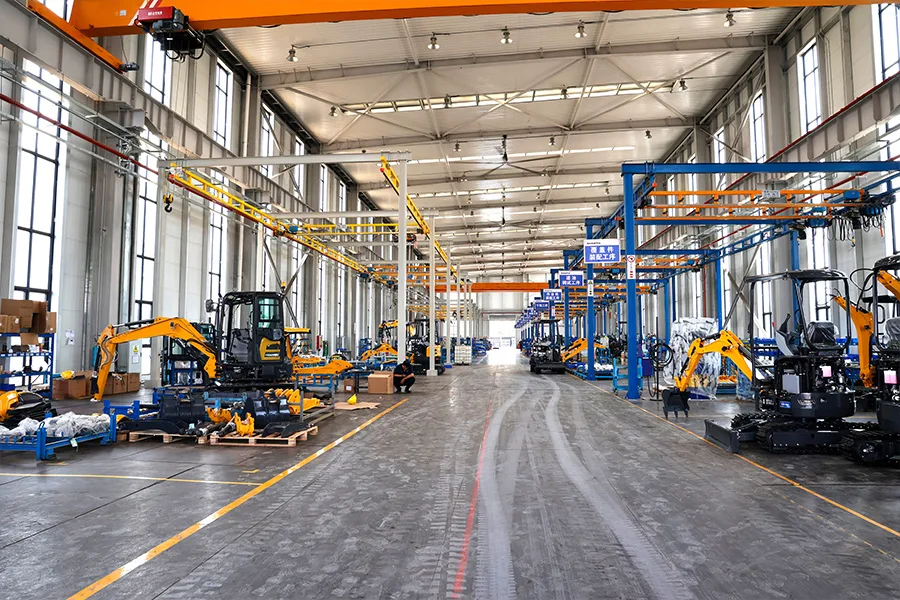
Accurate excavators are essential tools for many industries, from construction to mining and landscaping. These machines are prized for their precision and efficiency, enabling operators to complete complex tasks with great accuracy. However, like any advanced machinery, using accurate excavators requires a deep understanding of their features and limitations.
While accurate excavators offer tremendous advantages, there are common mistakes that can hinder their performance or lead to unnecessary expenses. These mistakes are often overlooked by operators or those unfamiliar with the nuances of operating such precise equipment. In this blog, we will discuss the six most common mistakes with accurate excavators and provide tips on how to avoid them.
By understanding and addressing these mistakes, operators can ensure they are getting the most out of their accurate excavators, avoiding costly repairs, downtime, and enhancing overall productivity.
NO 1. Not Regularly Calibrating the Excavator’s GPS System
Accurate excavators often come equipped with advanced GPS systems that help guide the machine with pinpoint precision. However, over time, these systems can experience drift or inaccuracies, especially if they are not regularly calibrated. Many operators make the mistake of assuming that the GPS system is always functioning optimally, but neglecting calibration can lead to errors in excavation depth, alignment, and even location.
The Importance of Regular Calibration
Calibration ensures that the excavator’s GPS system remains accurate, allowing the machine to maintain its precision. Without calibration, you might find that the excavator’s accuracy starts to deteriorate, causing issues such as misaligned diggings or incorrect positioning.
To avoid this mistake, always schedule routine calibration checks. If the excavator’s manufacturer provides a recommended calibration interval, follow it. Additionally, ensure that all components of the GPS system are well-maintained, including antennas and sensors.
NO 2. Failing to Inspect the Machine’s Hydraulic System
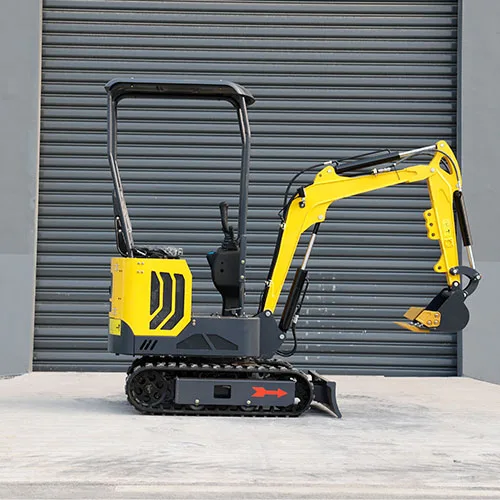
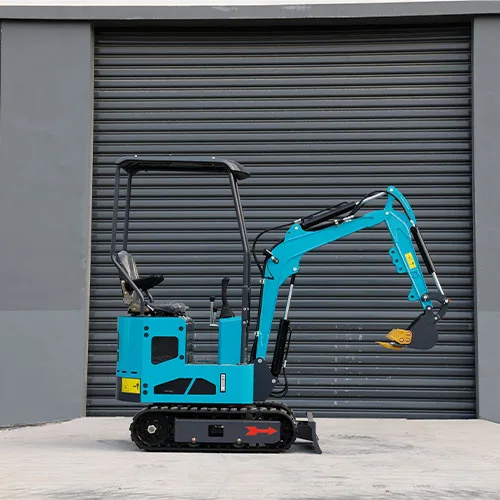
The hydraulic system in accurate excavators plays a crucial role in delivering the power necessary for precise movements. However, many operators fail to properly inspect the hydraulic components, leading to mechanical failures, decreased efficiency, or even total breakdowns. Over time, hydraulic fluid levels can decrease, or seals and hoses can deteriorate, causing leaks or performance issues.
Common Hydraulic Issues to Watch For
- Low hydraulic fluid levels
- Leaks in hoses or seals
- Damaged or worn-out hydraulic pumps
- Contaminated hydraulic fluid
Preventing Hydraulic Failures
To prevent these issues, always inspect the hydraulic system before and after each use. Regular maintenance and fluid changes can extend the lifespan of the hydraulic components and keep the excavator running smoothly. Additionally, operators should be trained to recognize the signs of potential hydraulic issues early on, such as unusual noises or erratic movement in the arm or bucket.
NO 3. Ignoring Proper Load Distribution
One of the most common mistakes with accurate excavators is improper load distribution. Overloading or uneven loading can cause the excavator to become unstable, leading to accidents or equipment damage. Even though accurate excavators are designed to handle large loads, distributing the weight unevenly can strain the machine and affect its performance.
How Load Distribution Affects Accuracy
Inaccurate load distribution can cause the excavator to tilt, affecting its ability to perform precise movements. This could lead to issues such as uneven digging, incorrect depth, or even damage to the arm and other parts of the excavator. When operating an accurate excavator, always ensure that the load is evenly distributed across the machine to maintain stability and performance.
Tips for Proper Load Distribution
- Always balance the load evenly across the bucket or attachment.
- Be mindful of the load’s center of gravity, ensuring it is as low as possible.
- Avoid overloading the machine beyond its rated capacity.
NO 4. Neglecting Proper Machine Maintenance
Another common mistake is neglecting regular maintenance. Accurate excavators are complex machines that require frequent servicing to operate at peak performance. Ignoring routine maintenance can lead to a host of issues, from engine trouble to wear and tear on critical parts.
The Role of Preventative Maintenance
Preventative maintenance is crucial to maintaining the precision and longevity of accurate excavators. This includes checking for wear on parts like tracks, tires, and arms, as well as monitoring engine performance and fluid levels. Neglecting these regular checks can result in breakdowns that not only disrupt work but also lead to expensive repairs.
To avoid costly repairs and downtime, establish a maintenance schedule that includes daily, weekly, and monthly inspections. Keep a log of all maintenance performed and address any issues promptly.
NO 5. Not Training Operators on the Machine’s Capabilities
Accurate excavators are sophisticated machines with many features that can improve productivity and precision. However, operators who are not properly trained in using these features may not be able to take full advantage of the machine’s capabilities. Many mistakes arise simply from operators not understanding how to adjust settings or use advanced features like tilt rotators or GPS systems effectively.
The Importance of Operator Training
Proper training ensures that operators understand how to operate accurate excavators safely and efficiently. It also helps them understand how to use the machine’s advanced systems, such as its GPS and hydraulic controls, to achieve the desired results. Inadequate training can lead to errors, inefficiency, and even accidents on the job site.
Key Aspects of Training
- Familiarize operators with the machine’s advanced systems.
- Train operators on safety protocols to prevent accidents.
- Provide ongoing training to ensure operators stay up-to-date with the latest technology.
NO 6. Underestimating the Environmental Impact on Performance
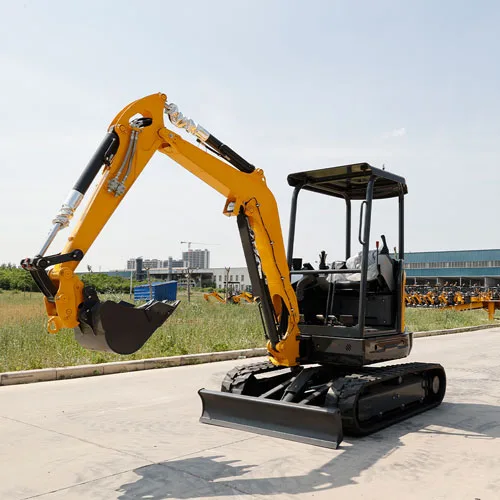
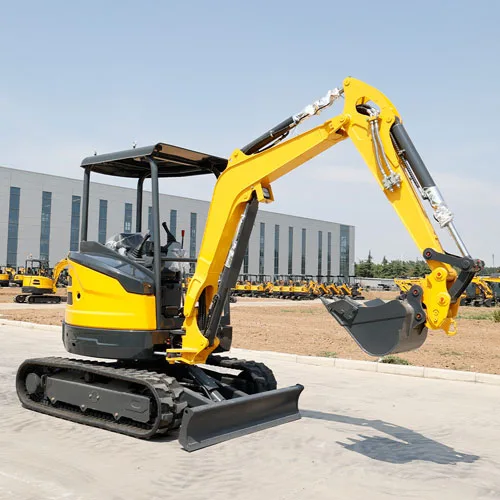
Environmental factors can have a significant impact on the performance of accurate excavators. Conditions such as extreme temperatures, high humidity, or rough terrain can affect the machine’s accuracy and efficiency. Many operators make the mistake of not considering how environmental factors may influence the performance of the excavator.
How Environmental Conditions Affect Excavators
- Extreme temperatures: Cold weather can cause fuel and hydraulic fluid to thicken, reducing efficiency. Hot weather can lead to overheating issues.
- Rough terrain: Uneven or soft ground can make it difficult for the excavator to maintain stability, affecting accuracy.
- High humidity: Moisture can corrode metal parts, causing rust and damage over time.
Tips for Managing Environmental Impact
- Regularly monitor the weather and ground conditions on the job site.
- Adjust machine settings to compensate for extreme weather.
- Use protective covers to prevent moisture damage when working in wet conditions.
Table: Common Mistakes with Accurate Excavators
Mistake | Consequences | Prevention Tips |
---|---|---|
Not calibrating GPS regularly | Misalignment, inaccurate excavation | Schedule routine calibration checks |
Failing to inspect hydraulic system | Hydraulic failures, performance issues | Regular inspections, fluid changes |
Improper load distribution | Instability, damage to the machine | Balance loads and monitor weight |
Neglecting maintenance | Reduced performance, breakdowns | Establish a regular maintenance schedule |
Lack of operator training | Errors, inefficiency, accidents | Provide thorough operator training |
Ignoring environmental factors | Reduced accuracy, corrosion | Monitor environmental conditions |
Conclusion
Accurate excavators are invaluable tools for many industries, providing the precision and efficiency needed to complete complex tasks. However, as with any heavy machinery, there are several common mistakes that can affect their performance. By addressing these mistakes—such as neglecting calibration, improper load distribution, and lack of maintenance—operators can ensure that their accurate excavators continue to perform at their best.
Proper training, regular inspections, and an understanding of how environmental factors affect the machine’s operation are also critical to avoiding costly errors. By implementing best practices, operators can maximize the efficiency and longevity of their excavators, ultimately boosting productivity and reducing downtime.
FAQ
How often should I calibrate my accurate excavator’s GPS system?
Calibration should be performed regularly, typically every few weeks or after significant changes in job site conditions. Follow the manufacturer’s recommendations for calibration intervals.
What are the signs that my excavator’s hydraulic system needs attention?
Look for signs such as sluggish movements, unusual noises, or leaking hydraulic fluid. Regular checks and fluid changes can prevent major hydraulic issues.
Can environmental factors really affect the accuracy of my excavator?
Yes, extreme temperatures, high humidity, and rough terrain can all impact the performance and accuracy of your excavator. Adjust settings and monitor conditions to minimize these effects.
What should I do if I notice irregular load distribution?
Immediately adjust the load to ensure it is balanced and within the machine’s rated capacity. This will prevent stability issues and potential damage.
Is operator training really necessary for using an accurate excavator?
Yes, proper training is crucial to ensure the operator can effectively use the machine’s advanced features and operate it safely, reducing errors and improving efficiency.