I’m thrilled to have you here! Before we dive into the content, let’s stay connected. Join me on my social media platforms for more insights, community engagement, and regular updates. Here’s where you can find me:
📌 Facebook: Shandong Huaying International Trade Co., Ltd.
Now, let’s embark on this journey together. I hope you find the content here not only insightful and engaging but also valuable to your interests. Let’s learn, grow, and connect!
Table of Contents
Introduction
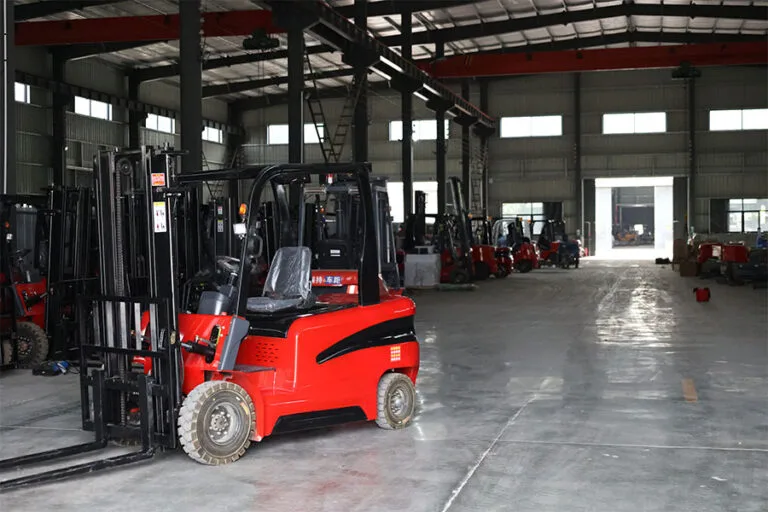
In the world of material handling, the sit down forklift remains a critical piece of equipment across industries. These machines offer operators comfort, stability, and enhanced control, making them an ideal choice for warehouses, manufacturing plants, and distribution centers. However, even the most robust sit down forklift cannot perform optimally if it is operated incorrectly.
Understanding how to avoid common mistakes when using a sit down forklift is essential for maintaining safety, improving productivity, and extending the life of the machine. In this blog, we will dive deep into the seven most frequent errors operators and managers make, how they can negatively impact operations, and what you can do to prevent them.
By mastering proper sit down forklift practices, businesses can minimize costly accidents, avoid downtime, and create a safer working environment for everyone involved.
1. Overloading the Sit Down Forklift Beyond Its Capacity
One of the most frequent and dangerous mistakes is overloading the sit down forklift. Every machine has a specified load capacity, and exceeding it can result in severe consequences.
Overloading can compromise the forklift’s balance, causing tip-overs and making it harder to control. Not only does this endanger the operator, but it also puts nearby workers at risk. The weight imbalance can also lead to mechanical wear and tear, shortening the machine’s operational life.
Operators must always check the load capacity rating and never assume that the sit down forklift can handle “just a little more.” Proper load distribution techniques and regular training can prevent these dangerous incidents from occurring.
2. Neglecting Regular Maintenance
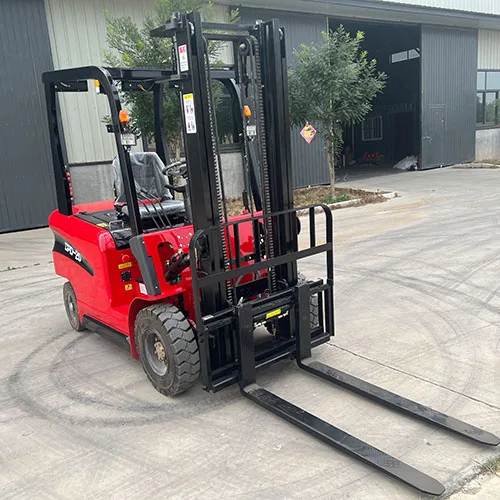
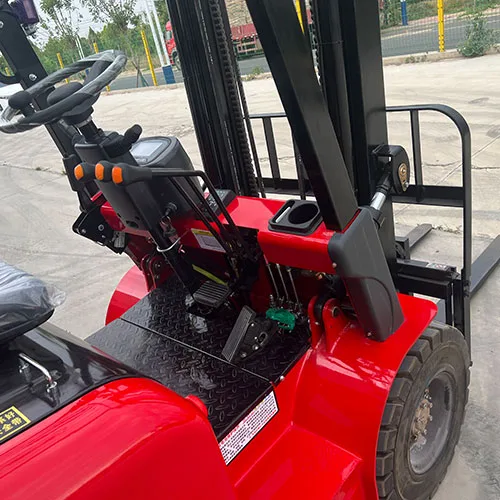
Ignoring maintenance schedules is another significant error many businesses make. Sit down forklifts, like any heavy machinery, require routine inspection and servicing to operate efficiently and safely.
Maintenance includes checking brakes, tires, hydraulic systems, and lifting mechanisms. Neglecting these can lead to sudden mechanical failures during operation, putting lives and products at risk.
Below is a table illustrating common maintenance tasks and their recommended frequency for a sit down forklift:
Maintenance Task | Frequency | Importance |
---|---|---|
Brake Inspection | Weekly | Ensures the forklift can stop effectively |
Hydraulic Fluid Check | Weekly | Prevents lifting malfunctions |
Tire Condition and Pressure | Bi-weekly | Maintains stability and mobility |
Full System Inspection | Monthly | Detects hidden issues early |
Battery and Charging System | Daily (for electric models) | Ensures uninterrupted operation |
Establishing a preventive maintenance program is critical for maximizing the longevity and performance of your sit down forklift fleet.
3. Operating the Sit Down Forklift at Unsafe Speeds
Another critical mistake is operating this type of forklift too fast, especially in tight aisles or crowded warehouse spaces. Unlike standard vehicles, lift trucks have a much higher center of gravity, making them far more susceptible to tipping during sharp turns or abrupt stops.
Driving at excessive speeds dramatically reduces the operator’s reaction time, increasing the likelihood of collisions and workplace accidents. This behavior becomes particularly hazardous in busy environments where pedestrians, shelving, and other machinery are present.
To mitigate these risks, supervisors should enforce strict speed limits throughout the facility and ensure that all drivers are fully aware of the dangers associated with reckless operation. Fortunately, many modern units come equipped with programmable speed controls that can automatically limit travel speeds. Utilizing these built-in safety features is a smart way to encourage responsible driving habits and create a safer workspace for everyone.
4. Improper Use on Uneven Surfaces
A warehouse forklift is primarily engineered for use on smooth, flat surfaces. Attempting to drive it across rough, bumpy, or sloped terrain is a serious misuse that can easily result in loss of stability or even mechanical damage.
When one of these vehicles is forced to navigate potholes, gravel patches, or slanted floors, the risk of a tip-over increases significantly. In addition to safety concerns, uneven ground places unnecessary strain on the tires, hydraulic systems, and frame components, leading to premature wear and costly repairs.
Before beginning any task, operators should carefully assess the work environment and ensure that the machine is only used where it is designed to perform safely. In cases where operations must be conducted outdoors or over rugged ground, switching to a rough terrain forklift is a much wiser and safer choice.
5. Failing to Secure Loads Properly on the Sit Down Forklift
Ensuring that loads are properly secured before transport is a fundamental rule of forklift operation that is too often neglected. Simply resting cargo on the forks without stabilization creates a major risk of load shifts, spills, or total tip-overs during transit.
Poorly secured goods endanger not just the driver, but also other personnel and valuable inventory around the facility. Unexpected movements of cargo can cause serious accidents, operational delays, and significant financial loss.
Operators should always verify that items are evenly balanced, centered on the forks, and adequately restrained before moving. This may involve using additional tools such as load straps, shrink wrap, or specialized pallet attachments. By taking a few extra minutes to secure each load correctly, drivers can greatly enhance stability and ensure a much safer transport process.
6. Lack of Proper Training and Certification for Sit Down Forklift Operators
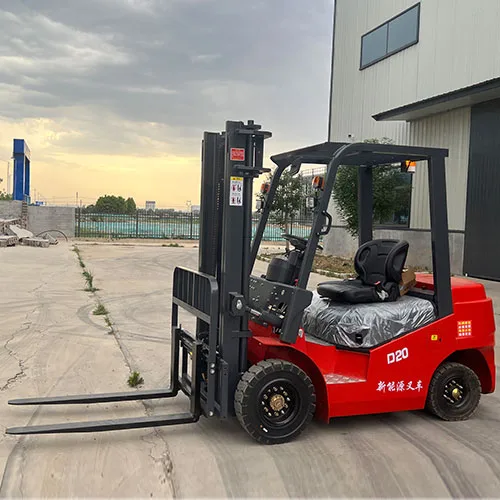
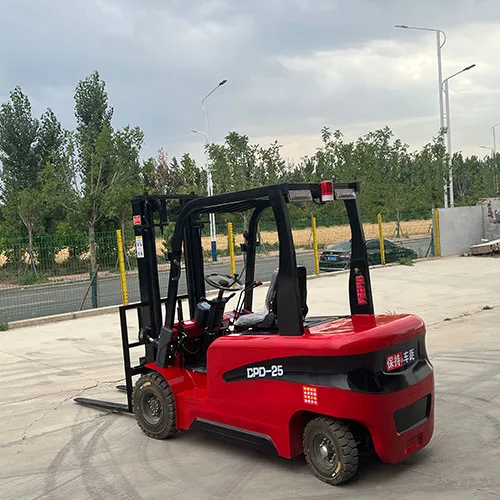
Allowing untrained or uncertified individuals to operate warehouse equipment is one of the most dangerous errors a company can make. Proper training is not merely recommended; it is a legal obligation under OSHA standards and critical for workplace safety.
Operators who have not undergone sufficient instruction may be unaware of basic safety practices, correct load handling methods, or emergency procedures. This lack of knowledge leads to poor decision-making and dramatically increases the probability of workplace incidents and injuries.
Employers must guarantee that every driver is properly certified and participates in regular refresher courses to maintain their skills and awareness. Investing in comprehensive training programs not only ensures legal compliance but also boosts overall operational efficiency and reduces the likelihood of costly accidents.
7. Ignoring Environmental Conditions While Operating a Sit Down Forklift
Many forklift operators neglect to account for changing environmental conditions, a mistake that can quickly compromise safety. Factors such as lighting quality, floor surface conditions, and seasonal weather variations all have a profound impact on equipment handling.
For instance, a wet or oily warehouse floor can reduce tire traction, making it easier to lose control of the vehicle. Similarly, poor lighting conditions can obscure hazards, shelving, or foot traffic from an operator’s view, increasing the risk of collisions.
Operators should make it a habit to evaluate their surroundings at the start of every shift and adjust their driving techniques accordingly. This could involve slowing down, taking wider turns, or being extra cautious when handling loads. A heightened sense of environmental awareness not only prevents accidents but also ensures a smoother, more efficient workflow across the facility.
Conclusion
Using a sit down forklift effectively requires more than just knowing how to drive—it demands a commitment to best practices, regular maintenance, and proper training. Avoiding the seven common mistakes outlined in this article will significantly improve the safety, performance, and longevity of your sit down forklift operations.
By prioritizing training, respecting load capacities, maintaining the equipment, and being mindful of environmental conditions, businesses can reap the full benefits that a sit down forklift offers. A small investment in awareness and prevention today can save thousands of dollars and countless hours in the future.
Make safety and efficiency your top priorities, and your sit down forklift fleet will serve your operations well for years to come.
FAQ
What is the load capacity of a typical sit down forklift?
The load capacity of a sit down forklift typically ranges from 3,000 to 6,000 pounds. However, it’s crucial to consult the manufacturer’s specifications for the exact rating of your specific model.
How often should a sit down forklift be inspected?
A sit down forklift should undergo daily pre-shift inspections and more comprehensive inspections on a monthly basis to ensure optimal performance and safety.
Can a sit down forklift be used outdoors?
While a sit down forklift is designed primarily for indoor use on smooth surfaces, it can be used outdoors on flat and paved surfaces. It is not ideal for rough or uneven terrain.
Why is speed control important when operating a sit down forklift?
Controlling speed is critical because a sit down forklift has a higher center of gravity, making it more prone to tipping over when driven too fast, especially around corners.
What should I do if a sit down forklift tips over?
If a sit down forklift begins to tip over, the operator should stay inside the cab, brace themselves, and lean away from the direction of the fall. Jumping out can lead to more serious injuries.