Welcome to My Blog!
I’m thrilled to have you here! Before we dive into the content, let’s stay connected. Join me on my social media platforms for more insights, community engagement, and regular updates. Here’s where you can find me:
📌 Facebook: Shandong Huaying International Trade Co., Ltd.
Now, let’s embark on this journey together. I hope you find the content here not only insightful and engaging but also valuable to your interests. Let’s learn, grow, and connect!
Table of Contents
Introduction
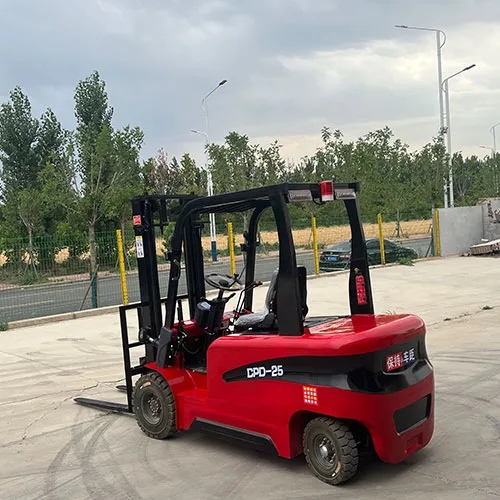
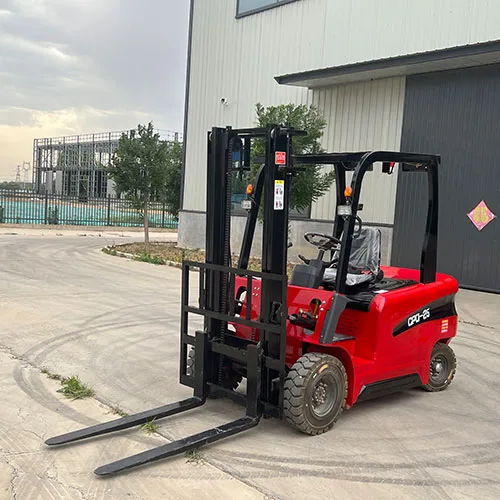
In the demanding environment of construction sites, precision and safety are paramount. Among the essential tools found on these sites, the construction forklift stands out for its versatility and utility. However, despite its benefits, misuse or mismanagement of this equipment can result in significant problems ranging from injuries to financial loss.
Mistakes involving a construction forklift aren’t just minor issues—they can halt a project, damage materials, and put lives at risk. This article provides an in-depth look into four common but costly mistakes operators and site managers make with construction forklifts and practical advice on how to avoid them.
Whether you’re a site supervisor, equipment manager, or forklift operator, understanding and avoiding these mistakes will enhance your site’s efficiency, protect your investment, and ensure a safer workplace.
Mistake #1: Choosing the Wrong Type of Construction Forklift
Selecting the incorrect model or type of forklift can cause delays, damage, or underperformance. Each construction site presents different challenges, and using a machine not suited to those conditions can lead to inefficiencies and increased operating costs.
How to Choose the Right Forklift for Your Site
Construction forklifts vary by type, capability, and suitability for different terrains and loads. Making the right choice involves considering several key factors:
- Site terrain: Is it rough or smooth?
- Load size: How much weight will you lift regularly?
- Height requirements: How high must materials be placed?
- Space constraints: Is maneuverability a concern?
Different types of construction forklifts serve different purposes. For example:
- Telehandlers are ideal for lifting materials to higher levels.
- Rough terrain forklifts are built for outdoor and uneven surfaces.
- Straight mast forklifts work well on compact or flat construction zones.
Assessing your needs before making a purchase or rental decision will prevent future complications, such as mechanical strain or restricted access to critical work areas.
Mistake #2: Skipping or Delaying Construction Forklift Maintenance
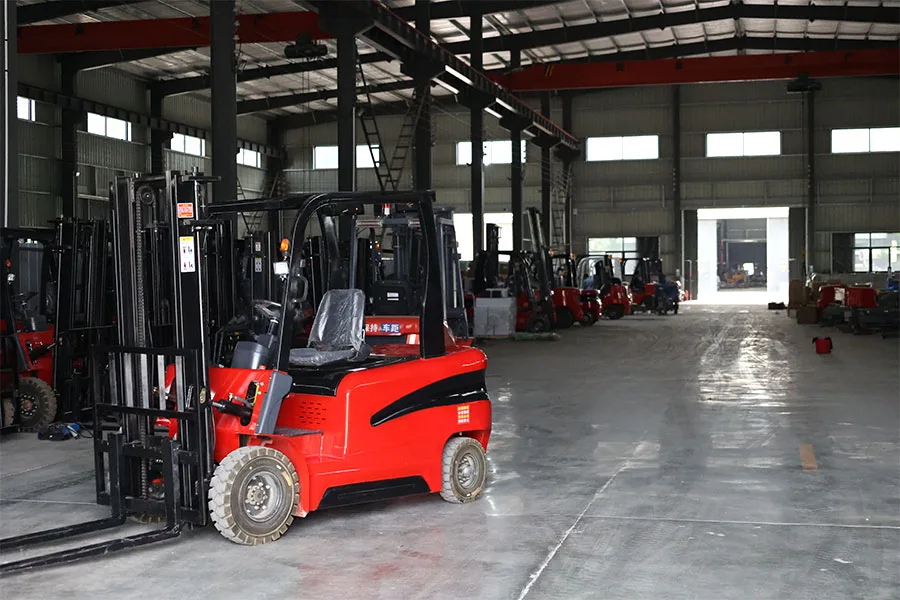
Routine maintenance is not optional—it is vital. A common yet dangerous mistake is neglecting forklift care. Regular inspection and servicing keep equipment in good working condition and prevent accidents.
Why Regular Maintenance Matters
Construction forklifts endure harsh conditions, from exposure to dirt and debris to carrying heavy loads multiple times per day. These tasks naturally wear down components. When left unchecked, even small issues can escalate into major failures.
Maintenance schedules should include checks for:
- Tire condition and inflation
- Hydraulic system pressure and leaks
- Brake responsiveness
- Oil and coolant levels
- Lift chain tension
- Electrical systems
Below is a maintenance schedule for optimal forklift performance:
Maintenance Task | Frequency | Purpose |
---|---|---|
Visual inspection | Daily | Detect fluid leaks, tire damage, or broken lights |
Tire pressure check | Weekly | Maintain balance and reduce wear |
Hydraulic fluid inspection | Every 100 hours of use | Prevent pressure loss and component failure |
Engine oil change | Every 250 hours of use | Ensure engine performance |
Brake inspection | Monthly | Guarantee stopping capability |
Full mechanical inspection | Every 6 months | Catch internal wear and prolong lifespan |
Failing to follow this schedule could result in breakdowns during crucial operations and cause project delays.
Mistake #3: Insufficient Operator Training and Certification
Another common issue is putting forklifts in the hands of individuals who aren’t fully trained or certified. Lack of training can lead to unsafe practices, costly errors, and legal violations.
Training Is More Than Just a Form Requirement
Operating a construction forklift involves understanding more than just the controls. An operator must grasp concepts such as:
- Load capacity and load center
- Turning radius and stability
- Site-specific risks like elevation or visibility
- Emergency stop procedures
Most countries and regions mandate proper training and certification before operating heavy machinery. Certified training often includes both classroom and hands-on instruction, ensuring that the operator can manage equipment in various situations.
Companies that skip this training to save money often end up spending more in accident claims, equipment repair, and insurance premiums.
Continuing Education
Forklift operation guidelines and technologies evolve. Encourage operators to attend refresher courses or advanced training programs to stay up-to-date.
Mistake #4: Overloading the Construction Forklift
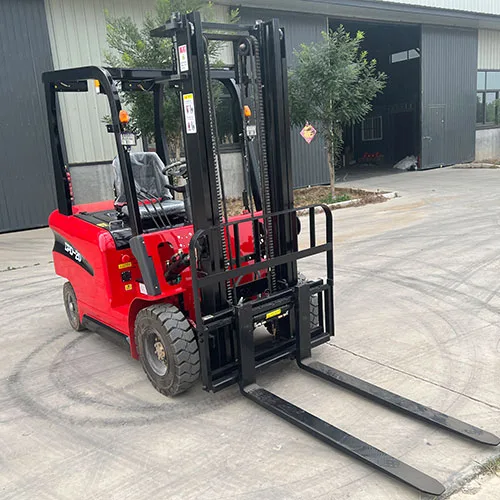
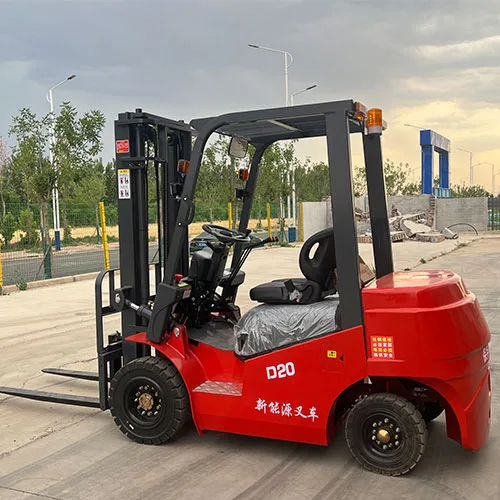
Overloading is a dangerous and avoidable mistake. It compromises the structural integrity of the forklift, puts strain on the hydraulics, and creates a significant tipping risk.
Understand Load Limits and Load Charts
Each forklift comes with a manufacturer-specified load chart. This chart shows how much weight the machine can safely lift at various heights and distances.
Factors influencing lifting capacity include:
- Load center: The closer the load is to the mast, the more stable the lift.
- Height: Higher lifting reduces stability.
- Attachments: Fork extensions and other add-ons change the center of gravity.
Consequences of overloading include:
- Forklift tipping over
- Damaged forks or lift mast
- Load dropping and injuring workers
- Immediate loss of balance, especially on uneven terrain
To prevent this:
- Always know the weight of the load before lifting
- Use weighing equipment if unsure
- Train operators to check the forklift’s load chart regularly
Avoiding this mistake not only preserves the equipment but also prevents tragic incidents on site.
Additional Safety and Efficiency Practices for Forklift Use
Avoiding individual mistakes is important, but so is building a proactive safety culture. Integrating smart practices helps reduce forklift-related risks across the board.
Implement a Forklift Safety Policy
Establishing a written safety plan, complete with rules, expectations, and procedures, is essential. Include details on:
- When and how forklifts are to be operated
- Maintenance and inspection requirements
- Communication protocols between operators and other workers
Designate Clear Travel Paths
Many construction sites are busy and cluttered. Designate specific lanes for forklift travel to avoid pedestrian interaction and create visual boundaries using cones or painted lines.
Equip Forklifts with Modern Technology
Newer forklift models or add-ons allow for digital load tracking, GPS monitoring, and collision avoidance alerts. These features can reduce risks and increase efficiency in high-traffic or low-visibility areas.
Monitor Usage and Behavior
Use telematics or operator logbooks to monitor forklift activity. Track usage patterns, idle times, and load trends to identify inefficiencies or risky behavior early.
Maintain Communication Between Teams
Encourage open dialogue between project managers, forklift operators, and site workers. If an issue is noticed—such as poor visibility, slick surfaces, or unclear travel paths—it should be reported immediately.
Conclusion
Using a construction forklift correctly can streamline project workflows and reduce manual labor. But one wrong move, one missed check, or one untrained operator can lead to setbacks that cost far more than they save.
Avoiding the four major mistakes outlined in this article—selecting the wrong equipment, skipping maintenance, neglecting training, and overloading—will position your team for success. These aren’t just tips; they are essential practices that can prevent costly delays, injuries, and equipment failures.
A construction site thrives on organization, preparation, and communication. Let those same values guide your approach to construction forklift management.
FAQ
What is a construction forklift primarily used for?
It is used to lift and transport heavy materials across a job site. These forklifts can be fitted with various attachments for lifting pallets, construction materials, and tools.
How often should I inspect my construction forklift?
Daily visual checks should be conducted before each shift. Full mechanical inspections should be done every 6 months, with additional routine checks scheduled based on usage.
Can I use any forklift on a construction site?
Not all forklifts are suitable. Rough terrain and telehandler forklifts are best for outdoor construction work. Using the wrong type can result in equipment failure or accidents.
What is the best way to prevent overloading?
Refer to the forklift’s load chart, use load scales if available, and train operators on safe load handling. Never guess the weight of a load.
Do all forklift operators need certification?
Yes. Most regions require certification for legal and safety compliance. Certified operators reduce accident risks and are often more efficient in operation.
What are common signs that a forklift needs maintenance?
Unusual noises, leaking fluids, slow lift operation, warning lights, or visible wear on tires and forks are all red flags. Any of these should be addressed before continued use.
Should I rent or buy a forklift for construction?
If you need it short-term or for one project, renting may be more cost-effective. For ongoing needs, purchasing can offer better long-term value.