Welcome to My Blog!
I’m thrilled to have you here! Before we dive into the content, let’s stay connected. Join me on my social media platforms for more insights, community engagement, and regular updates. Here’s where you can find me:
📌 Facebook: Shandong Huaying International Trade Co., Ltd.
Now, let’s embark on this journey together. I hope you find the content here not only insightful and engaging but also valuable to your interests. Let’s learn, grow, and connect!
Table of Contents
Introduction
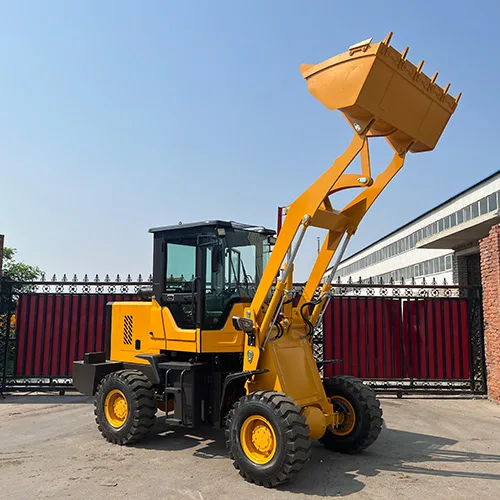
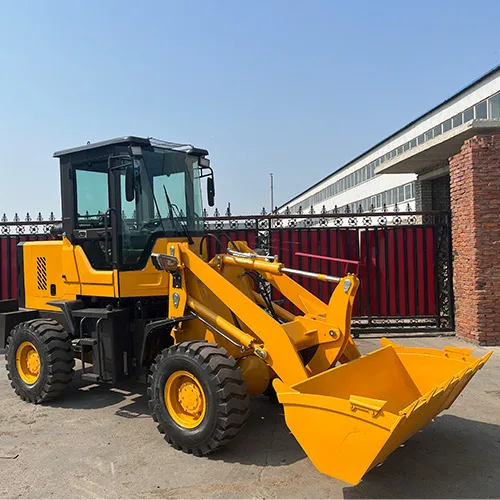
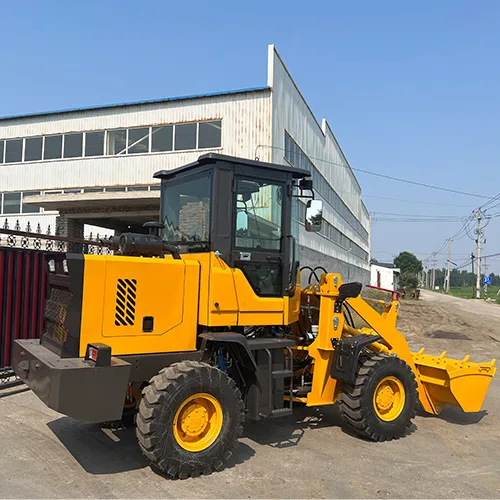
Wheel loaders are among the most versatile and essential pieces of heavy equipment in industries such as construction, mining, agriculture, and material handling. These powerful machines are designed to move massive amounts of dirt, gravel, and other materials efficiently. However, like any heavy-duty equipment, wheel loaders require consistent maintenance to perform at their best.
Neglecting routine maintenance can lead to unexpected breakdowns, costly repairs, and even premature replacement—costing businesses thousands of dollars in lost productivity and repair bills. In this comprehensive guide, we’ll explore why proper wheel loader maintenance is a smart investment, how it extends machine lifespan, and what key tasks should be prioritized to avoid expensive downtime.
The True Cost of Neglecting Wheel Loader Maintenance
1. Unexpected Downtime Leads to Lost Revenue
When a wheel loader breaks down unexpectedly, operations come to a halt. In industries where time equals money, even a few hours of downtime can result in significant financial losses.
- Example: A construction site relying on a wheel loader to move materials may face delays in project timelines, leading to penalties or overtime labor costs.
- Solution: Scheduled inspections and preventive maintenance reduce the risk of sudden failures.
2. Major Repairs Are Far More Expensive Than Routine Maintenance
A small issue, such as a leaking hydraulic hose, can escalate into a catastrophic failure if ignored.
- Cost Comparison:
- Replacing a hydraulic hose early: 200−200−500
- Waiting until the hose bursts, damaging the pump: $3,000+
3. Reduced Resale Value
A well-maintained wheel loader retains a higher resale value. Buyers prefer machines with documented service histories, knowing they won’t face immediate repair costs.
Essential Wheel Loader Maintenance Tasks
1. Daily Inspections (Operator-Checked Items)
Before each shift, operators should perform a quick inspection to catch potential problems early.
Checklist Item | Why It Matters |
---|---|
Engine Oil Level | Low oil causes engine wear |
Hydraulic Fluid Level | Prevents pump failure |
Tire Pressure & Condition | Uneven wear reduces efficiency |
Coolant Level | Prevents overheating |
Lights & Safety Features | Ensures worksite compliance |
2. Weekly & Monthly Maintenance
Beyond daily checks, deeper inspections should be performed weekly or monthly.
- Greasing Pivot Points: Reduces friction and wear on moving parts.
- Air Filter Cleaning/Replacement: A clogged filter reduces engine efficiency.
- Belt & Hose Inspection: Cracks or leaks can lead to sudden failures.
3. Scheduled Professional Servicing
Every 250-500 hours (or as per manufacturer recommendations), a certified technician should:
- Change engine oil and filters
- Inspect transmission and hydraulic systems
- Check wheel bearings and undercarriage components
Common Wheel Loader Problems & How to Prevent Them
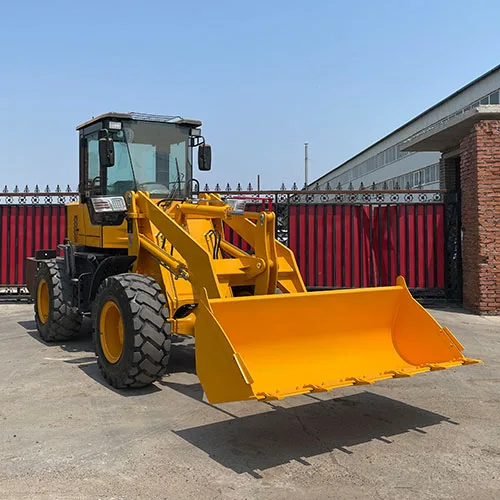
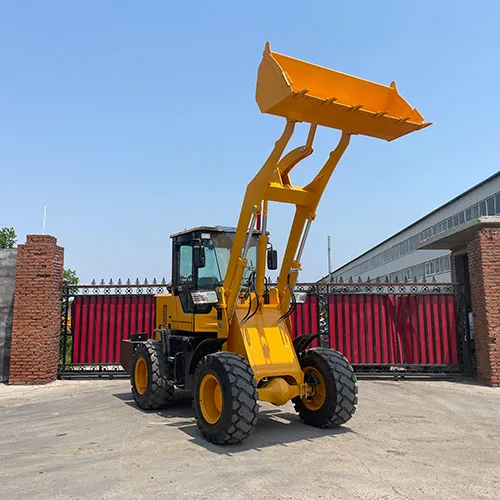
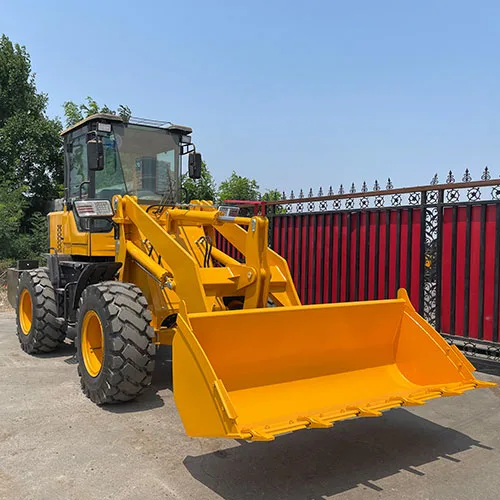
1. Hydraulic System Failures
Cause: Contaminated fluid, leaks, or worn seals. Prevention:
- Regularly check hydraulic fluid levels and quality.
- Replace filters as recommended.
- Fix leaks immediately to avoid pump damage.
2. Engine Overheating
Cause: Dirty radiators, low coolant, or faulty thermostats. Prevention:
- Clean radiator fins regularly.
- Use the correct coolant mixture.
- Monitor temperature gauges during operation.
3. Premature Tire Wear
Cause: Improper inflation, overloading, or rough terrain. Prevention:
- Maintain correct tire pressure.
- Rotate tires periodically.
- Avoid excessive spinning or harsh braking.
How Proper Maintenance Saves Money (Cost Breakdown)
Maintenance Task | Cost | Potential Repair Cost if Ignored |
---|---|---|
Oil & Filter Change | 150−150−300 | Engine failure (5,000−5,000−15,000) |
Hydraulic Hose Replacement | 200−200−500 | Pump replacement ($3,000+) |
Tire Replacement (Set) | 2,000−2,000−6,000 | Downtime + emergency replacement costs |
Greasing Bearings | 50−50−150 | Bearing failure ($1,500+) |
Total Potential Savings: Thousands per year by avoiding major repairs.
Conclusion
Investing in regular wheel loader maintenance isn’t just about avoiding breakdowns—it’s about maximizing efficiency, extending machine life, and protecting your bottom line. By following a structured maintenance schedule, businesses can:
✔ Reduce unexpected downtime
✔ Avoid expensive repairs
✔ Improve fuel efficiency
✔ Maintain higher resale value
Don’t wait for a breakdown to take action. Implement a proactive maintenance plan today and save thousands in the long run!
Need a customized maintenance checklist for your wheel loader? Contact our experts for a free consultation!
FAQ
How often should I change the hydraulic fluid?
Most manufacturers recommend changing hydraulic fluid every 1,000 hours, but check your equipment manual for exact intervals—harsh conditions like extreme heat or heavy dust may require more frequent changes.
Can I use aftermarket parts for repairs?
Aftermarket parts are cheaper, but OEM (Original Equipment Manufacturer) parts are usually more reliable, fit better, and often come with warranties, reducing long-term repair risks.
What’s the biggest mistake owners make?
Neglecting small maintenance tasks like greasing joints or checking fluid levels leads to faster wear and expensive breakdowns—consistent care prevents major issues.
How long should a well-maintained wheel loader last?
With proper maintenance, a wheel loader can last 10,000+ hours before needing major overhauls, but lifespan depends on usage, operating conditions, and timely servicing.